
Hammer & Crusher Attachments
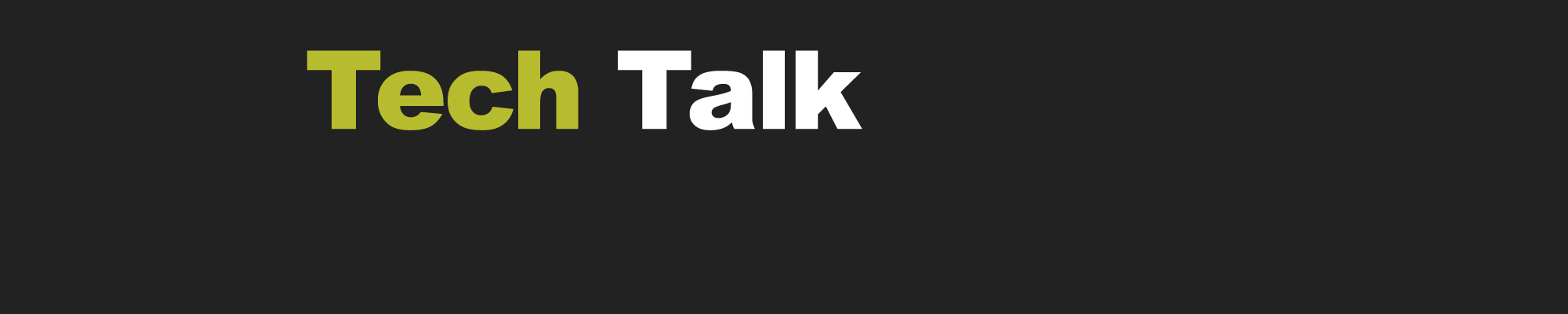
By Peter Bigwood
As demolition robots continue to take their place in the arsenals of concrete cutters across the country, attention turns to the variety of attachments that give them their reputation for versatility. There are generally five attachments that are widely considered to be the most popular: hydraulic breakers, crushers, buckets, grapples and scabblers. Hydraulic rock drills come in a close sixth. This article will focus on the two most popular: hydraulic breakers and concrete crushers.
Almost all remote-controlled demolition machines are delivered with hydraulic hammers mounted at the end of the arm as standard. In many ways, it can be said that demo robots are designed ‘backwards,’ starting with the breaker. Essentially, hydraulic breakers are ‘dumb’—that is, without oil flow and pressure from the carrier, appropriately low back pressure back to tank, and sufficient downward forces, they are useless.
And therein lies the secret of demolition robots—they are specifically designed to deliver exactly what the hammers demand, squeezing out close to 100% of the rated available performance. It’s what makes demolition robots so powerful for their size, but there are a number of measures to take to get the best out of the hammers.
A little preventative maintenance will go a long way towards extending the working life of the hammers typically found on demolition robots. While they are generally of the low-maintenance ‘solid body’ type, it is still critical to check all bolts, hoses, fittings and working tools on a daily basis.
Make sure that the tool steel is properly lubricated, with the correct manufacturer-recommended chisel paste. Ordinary grease is simply not adequate. True chisel paste, available from the hammer manufacturer, is a special formulation with copper and graphite particles that can withstand the extremely high heat and pressure generated inside the hammer. Robots come equipped with automatic lubrication systems, but technicians have come across situations where either they have been disconnected, or the chisel paste has been allowed to run out. There should always be evidence of the chisel paste seeping down about two inches at the top of the chisel, below the bushing. If it is dry, or if shiny spots can be seen on the surface, there is a problem. Additionally, on at least a monthly basis, inspect the tool and bushing to make sure they are both within the manufacturer’s operating parameters.
The working tools themselves are an oft neglected area where a little planning can go a long way. The most common hammer bit is the narrow chisel, but sometimes this is not the best choice. Note that a blunt chisel or even a flared out “elephant’s foot” can be far more effective at breaking up large expanses of concrete. A moiled point, by contrast, can be counter-productive in certain situations, burying itself in the material rather than propagating the desired cracking.
It is said that a demolition robot ‘makes its money’ on walls and ceilings. Unlike a mini-excavator, the geometry of the three-piece arm means that you can exert significant force at virtually any angle. When a job involves a good deal of breaking concrete overhead, a useful tip is to fashion a kind of shield for the hammer. Find an old piece of rubber, about a foot square, and cut an ‘X’ in the middle. Poke the chisel through the middle and slide the rubber piece up to the bushing. This will prevent the bulk of the concrete dust and debris from working its way into the bushing. While not ideal, even a thick piece of cardboard would help in a pinch. Note that solid body hammers do incorporate dust seals to help protect the tool and bushing area.
The rule of thumb for breaking concrete effectively is to hold the chisel at a 90 degree angle to the work. Straying from a right angle will reduce the impact power of the hammer. In certain circumstances, however, this can be used as an advantage. In an area where conditions call for reduced impact—to reduce the risk of micro-fractures, for example—purposely attack the surface at an angle. There are other, more formal ways to ‘dial down’ the impact energy of the breaker (consult the manufacturer’s operating manual), but this is a quick solution which can also work on a temporary basis.
When breaking concrete, if the tool point hasn’t penetrated the material after 30 seconds, stop and try for a smaller ‘bite’. Once an operator has determined the appropriately sized pieces, they can develop a good rhythm and increase productivity.
Next to breakers, hydraulic crushers are probably the second most popular attachment for demolition robots, and are especially useful for concrete cutting contractors. They are particularly effective in reinforced concrete and are productive in any position.
Designed specifically to match the flows and pressures available from the robot, crushers are compact enough to be maneuverable and precise in close quarters, but still pack an extraordinary amount of power for their size. Ideal for jobs in offices, schools or even hospitals, their single biggest advantage is that they are virtually silent when working and generate very little vibration. This makes interior demolition work in occupied space not only possible, but profitable. Dust can be controlled more effectively, and while productivity is not quite on par with hydraulic breakers, using crushers indoors allows the savvy contractor to manage overtime, control costs and complete jobs quickly.
There are a number of ways to get the best out of crushers and prolong their working lives.
Crushing tips and cutting heads should be inspected on a regular basis. They are replaceable, and should not be allowed to wear to the point where the underlying jaws are damaged.
A rule of thumb for crushers is that if the material fits in the jaw opening, it can be processed. An internal pressure booster kicks in when high resistance is encountered, and is generally able to break the concrete. Cutting surfaces near the throat can handle rebar up to one inch in diameter. It is important to let the crusher do the work, and NOT use the robot’s arm system to try to dislodge the material. Removing concrete and rebar in one bite and keeping the crusher against the work without repositioning makes for very high productivity.
Crushers rotate a continuous 360 degrees, but are ‘knock around’ style—the rotation is not powered by the carrier, but rather the operator ‘knocks’ the crusher around into the optimum angle of attack, where it will stay (note that a hydraulically-powered rotation option is also available). This procedure is much faster than positioning with hydraulic rotation and keeps tool weight low. It is important that when doing this, the operator avoids hitting the cylinders, but instead uses the tips of the jaws. This prevents damage to the cylinders, and offers more torque to rotate the attachment into the desired position. Unlike a breaker, the angle of attack for a crusher has no bearing on its ability to break the material.
Never operate the crusher with the robot’s arm’s cylinders at the end of their travel, as the forces the crusher can generate could damage the cylinder seals and bushings.
Much like eating a sandwich, it is preferable not to take a full ‘bite’ out of especially thick concrete, but rather leave room in the throat of the crusher for the material to move. On most crushers it is possible to add additional teeth, which makes them more effective for demolishing thinner concrete.
Demolition robots open new opportunities for concrete cutters to expand their capabilities in areas where access is limited, in confined space, in zero-emission places like occupied offices, schools and hospitals, and breakers and crushers play a critical role in all these applications. Attention to regular maintenance procedures, and focusing on sound operating principles will pay enormous dividends in deriving the greatest benefits from whichever size demolition robot is part of your fleet.
.